Tru‑Flex dostarcza podzespoły do najbardziej renomowanych marek pojazdów ciężarowych. Firma stanęła wobec potrzeby przeprowadzenia robotyzacji w swoim polskim zakładzie produkcyjnym. Celem było zdobycie kontraktu i zarazem zapewnienie regularnych dostaw o jednakowo wysokim poziomie jakości wytwarzanych produktów. Zdecydowano się na roboty spawalnicze Kawasaki, dostarczone przez ASTOR, a wdrożone przez firmę Robopartner.
Partnerem materiału jest Astor.
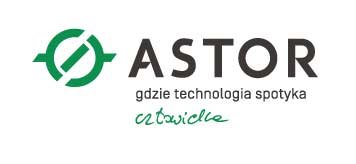
Tru‑Flex to renomowany producent części do samochodów ciężarowych. Firma działa od ponad 60 lat, a od ponad dekady dostarcza części bezpośrednio do montowni samochodów. Jest dostawcą komponentów do fabryk samochodów ciężarowych, pojazdów przemysłowych i rolniczych. O skali i jakości produkcji Tru‑Flex wiele mówi fakt, że co drugi samochód ciężarowy w Stanach Zjednoczonych jest wyposażony w układy wydechowe tej firmy. Wśród jej najważniejszych odbiorców są największe firmy z branży automotive. Od trzech lat Tru‑Flex jest obecny również w Polsce, jego zakład produkcyjny mieści się w miejscowości Zimna Wódka w województwie opolskim.
Konieczność robotyzacji
Nowy kontrakt na dostawę elementów układów wydechowych wymógł konieczność przeprowadzenia robotyzacji w polskich zakładach Tru‑Flex. Firmie zależało na zapewnieniu idealnej regularności dostaw produktów o powtarzalnie wysokim poziomie jakości. Wyzwanie nie należało do łatwych, ponieważ specyfika wytwarzanych produktów wymagała wdrożenia nowej technologii. Układ wydechowy w samochodzie ciężarowym musi wytrzymać 2–3 miliony kilometrów i temperaturę rzędu 700 stopni. Dla porównania, przewidywana żywotność układu wydechowego w samochodzie osobowym wynosi zaledwie 200 tysięcy kilometrów. Wymagania jakościowe układów wydechowych do ciężarówek stawiają producentów przed wyzwaniami zbliżonymi do tych, z którymi mierzą się producenci branży lotniczej. Zaangażowanie Tru‑Flex w sprostanie wymaganiom klientów potwierdza m.in. utrzymanie rygorystycznego systemu jakości ISO/TS.
Co więcej, układ wydechowy projektowany jest według wytycznych przekazanych przez producenta pojazdu. Konstrukcja geometryczna pojazdu jest w każdym samochodzie inna, więc praktycznie każdy projekt układu wydechowego jest prototypem. Komponenty układu nie tylko kompensują naprężenia spowodowane właściwościami fizycznymi materiałów (rozszerzalnością cieplną), lecz także chronią kosztowne systemy oczyszczania spalin przed nadmiernymi drganiami zarówno silnika, jak i kabiny kierowcy. Produkty Tru‑Flex są poddawane licznym rygorystycznym testom potwierdzającym przewidywaną długą żywotność produktu. Jego tajemnicę chroni ponad 40 patentów.
Uwolnij moc innowacji w swojej firmie» >
Ze względu na wyzwania technologiczne i czasowe firma zdawała sobie sprawę, że planowana robotyzacja będzie kluczowa dla podtrzymania i podnoszenia konkurencyjności przedsiębiorstwa. „Rozważając robotyzację, patrzymy na model biznesowy. W niektórych przypadkach, gdy wolumen produkcji jest odpowiednio wysoki, decydujemy się na roboty. Jest dla nas ważne, aby dostawcy – nasi udziałowcy, jak ich nazywamy – znali wymagania klientów i wiedzieli dokładnie, na czym nam zależy” – opowiada Paul Knaapen, dyrektor zarządzający Tru‑Flex Europe.
Dodatkowym wyzwaniem był wyjątkowo krótki czas przewidziany na stworzenie stanowisk zrobotyzowanych – cztery miesiące zamiast początkowo planowanych dwunastu.
Przemyślane wdrożenie
Do współpracy zaproszono firmę Robopartner, która specjalizuje się w robotyzacji spawania, szczególny nacisk stawiając na rozwój wiedzy i praktyki w zakresie zaawansowanych technologii spawania. „Potrzeba zwiększania mocy produkcyjnej, ograniczania przestojów oraz poprawa jakości i wydajności są obecnie przedmiotem zainteresowań coraz większej liczby przedsiębiorstw. Jest w tym sens – zwłaszcza gdy dotyczy to procesu spawania, który jest szczególnie podatny na robotyzację” – opowiada Mariusz Misztalski, właściciel firmy Robopartner, a zarazem technolog spawalnik.
Aby spełnić założenia projektu, należało zoptymalizować czas spawania kluczowych elementów oraz dostosować technologię do różnych gatunków stali nierdzewnej, z których miał powstać detal, tak aby zapewnić doskonałą jakość produktu końcowego. „W tym przypadku trudność procesu polegała na przetopieniu warstwy pięciu różnych materiałów jednocześnie w czasie zaledwie 30 sekund. Wykonaliśmy szereg testów, aby dobrać najwłaściwszą technologię” – wyjaśnia Mariusz Misztalski.
Dostarczono dwie tzw. cele zrobotyzowane, które zapewniają wysoki stopień uniwersalności. Każde stanowisko zrobotyzowane posiada dwie strefy pracy – w jednej jest realizowany proces spawania, a w drugiej następuje wymiana detali przez operatora przy zachowaniu najsurowszych norm bezpieczeństwa. Przyrządy spawalnicze mogą być naprzemiennie wymieniane w dowolnej strefie pracy. Pozwala to na elastyczne wykorzystywanie maszyn do aktualnej produkcji poszczególnych referencji. Ułatwieniem jest system samodzielnego wykrywania danego przyrządu spawalniczego przez robota, co eliminuje potencjalne awarie spowodowane błędnym wyborem programu przez operatora. Całość sprowadza się jedynie do wypięcia wtyczki przemysłowej podmiany przyrządu, i ponownego wpięcia wtyczki nowego przyrządu.
„Tempo i wydajność produkcji muszą być nieustannie optymalizowane, bez kompromisów w sferze jakości. W tym procesie niewątpliwym wsparciem jest robotyzacja spawania” – mówi Andrzej Garbacki, członek zarządu operacyjnego w firmie ASTOR.
„Do budowy stanowisk użyliśmy sprzętu sprawdzonych producentów – takich jak m.in.: roboty Kawasaki z pozycjonerami ASTOR, zestawy spawalnicze Fronius CMT, szybkobieżne bramy Albany Assa Abloy, jednostki filtracyjne Kemper. Zależało nam również, aby stanowiska były niezawodne, bezpieczne i zapewniały klientowi najwyższą funkcjonalność. Dlatego już na etapie projektowania przemyśleliśmy takie rozwiązania, jak: automatyczne wykrywanie przyrządów spawalniczych przez robota, centralny panel sterujący, wspólna platforma podłogowa czy zintegrowana filtrowentylacja” – wylicza Mariusz Misztalski.
Potrzeba zwiększania mocy produkcyjnej, ograniczania przestojów oraz poprawa jakości i wydajności są obecnie przedmiotem zainteresowań coraz większej liczby przedsiębiorstw. >
TweetnijZa bezpieczeństwo odpowiada certyfikowany system Kawasaki Cubic‑S, który nadzoruje pracę robota, pozycjonerów i współpracuje z urządzeniami zabezpieczającymi. „W nowoczesnych zakładach produkcyjnych sprawą najwyższej wagi jest zapewnienie elastyczności działania, tak aby móc szybko reagować na wymagania i potrzeby rynku. Tempo i wydajność produkcji muszą być nieustannie optymalizowane, bez kompromisów w sferze jakości. W tym procesie niewątpliwym wsparciem jest robotyzacja spawania” – komentuje Andrzej Garbacki, członek zarządu operacyjnego w firmie ASTOR.
Mimo złożoności i skali trudności przedsięwzięcia przedstawiciele firmy Tru‑Flex przyznają, że założone cele udało się zrealizować z nawiązką. „Wysokie zapotrzebowanie ilościowe, perfekcyjna regularność dostaw i oczekiwany najwyższy, powtarzalny poziom jakości spowodowały konieczność realizacji projektu przy wsparciu robotyzacji. Udało się osiągnąć wydajność i powtarzalność spawania lepszą, niż to było wstępnie zakładane” – uważa Jarosław Szytow, dyrektor zakładu produkcyjnego Tru‑Flex Polska.
PRZECZYTAJ TAKŻE: Automatyzacja i robotyzacja – symbole rewolucji Przemysłu 4.0 » >